Simple and robust design measures parts dynamically in a variety of applications.
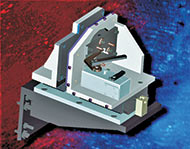
-
Specifications
- Thickness range:
-
2.3mm to 38mm
.09" to 1.5" - Thrufeed rate:
-
2.5 to 7.5 meters/minute
100 to 300 inches/minute - Diameter, height, weight:
- 25mm to 125mm, 1" to 5" for both
The DDP concept is simple: a circular, spring-loaded gaging shoe presses the ground part against a precise reference surface. The gage contacts the back of the shoe, sending the measured thickness of the part to the D500 Gage Controller.
Workpieces may be carried or pushed through the fixture in several different ways, including rotary carrier, swing arm, or custom mechanism. Our specialized "Micropeak" software analyzes the dynamic gage signal (which is rising and falling with the gage shoe), then calculates precise part size. The D500 monitors size relative to target, then compensates the machine based on a scheme "tuned" to your application.
DDP fixtures are designed for the gritty, swarf-filled world of grinding. Fixture components that touch the workpiece are highly hardened or titanium hardcoated. And the measuring head is one of CGI's exclusive quick-setup slipclutch gages, not a fragile pencil probe. Our gage heads are not only precise (repeatability to .0005mm (.000020") but are specifically designed to - and do in fact - last for years in the harsh grinding environment.
There are already application drawings for multiple machines and part types, and the DDP can typically be designed into new situations at very reasonable cost.
DDP Disc Grinder Gaging Fixture (PDF)
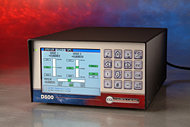
The D500 Gage Controller provides a range of software methods for trend-based size control. The advanced IPC option (Intelligent Process Control) significantly outperforms all other compensation techniques, and can control a machine to its best possible operating capability.